|
Mechanical seal pumps
Mechanical seals - also referred to as dynamic seals -
are used to seal rotating shafts against a wall, e.g. a pump casing. The
mechanical seal consists of two main components sliding on one another, the
spring-loaded stationary seal ring and the rotating seal ring.
One of the two seal rings is rigidly mounted in the stationary part, the
other is mounted on the rotating shaft. Depending on the type of mechanical
seal, the faces of these two seal rings are usually flat and fabricated from
materials such as carbon-graphite, metals, ceramics, plastics or
resin-reinforced carbon.
Mechanical seals are normally designed
as axial seals.
The two mating axial sealing faces rotate relative to one
another, forming a primary clearance. Depending on its physical state, the
surrounding medium forms a liquid lubricant film between the sealing faces.
Sealing of the mechanical seal components against the shaft or casing is
normally accomplished by secondary seals in the form of additional O-rings or
collars. Accordingly, mechanical seals consist of five
components: the stationary seal ring, the rotating seal ring,
the spring chamber and one secondary seal each. Depending on the specific
mechanical seal design, the number of components may be smaller or also
significantly larger.
The stationary and rotating seal ring faces are made of
dissimilar materials, the material combination being critical to the performance
of the mechanical seal. Factors governing the
material selection for the rotating and stationary seal rings are the fluid to
be contained, the speed of rotation and the service temperature.
With mechanical seals, a distinction is made between hard-hard or
hard-soft material pairings. A hard-soft material pairing
designates a combination of sliding components where one sliding face is
significantly softer than its sliding partner and therefore wears down more
easily while offering better dry run characteristics during unfavourable
lubricating conditions. A typical combination is a carbon ring sliding on a
silicon carbide ring. In hard-hard material pairings, both seal rings are made
of hard and wear-resistant material, e.g. silicon carbide (SIC). This
combination is mainly used in abrasive service environments because of its
superior wear resistance, however at the expense of poor dry run capabilities.
Besides the material pairing, the absolute flatness of the sealing faces and the
surface roughness are of decisive importance for the sealing performance and
wear resistance. Normally, the sealing faces are lapped, polished and, where
required, provided with a super finish.
Pumps for the most diverse service environments are a key
application of mechanical seals. These days mechanical seals
are available for shaft diameters from about 5 to 630 mm, pressures from about
0.01 to 300 bar, temperatures from about – 200 to + 450 °C and sliding rates of
up to about 150 m/s.
There will always be some leakage from a mechanical seal,
even though the leakage rate is small. This is unavoidable since the seal rings
have to be lubricated to carry off the heat of friction. As mechanical seals are
normally product-lubricated, there will inevitably be some minor leakage.
There are, however, applications where it is absolutely
necessary to avoid leakage from the shaft seal. Typical examples are toxic,
explosive, carcinogenic, mutagenic fluids or fluids posing a health or
environmental hazard or having other critical properties.
To ensure reliable product containment, double mechanical
seals operated with buffer fluid are used in such applications. These seals
consist of two tandem-arranged mechanical seals. The clearance so created is
flushed with a buffer medium having a pressure above that of the product to be
contained.
TA-Luft prescribes the use of pumps with double mechanical
seal or even hermetically sealed pumps to preclude any health or environmental
risks when pumping liquids having the above characteristics.
Munsch pumps are available as single
mechanical seal pumps and double mechanical seals pumps. Typical features of the
Munsch mechanical seal are its simple construction and ease of assembly and
disassembly.
The REA mechanical seal specifically
developed for our non-metallic pumps features maximum operating reliability, a
long service life while being easy to assemble and repair.
The main construction material of the mechanical seal is silicon carbide which
is unmatched in its corrosion and wear resistance.
MUNSCH-REA-F single mechanical seal:
The rotating and stationary seal rings
are fabricated from silicon carbide; the spring is provided with a
fluoroplastics coating.
MUNSCH-REA-F/D double mechanical seal:
The product-side stationary and rotating
seal rings as well as the atmosphere-side rotating seal ring are fabricated from
silicon carbide; the atmosphere-side stationary seal ring is made of carbon, the
spring of stainless steel.
MUNSCH-REA mechanical seal with spring
chamber flushing (option)
A spring chamber flushing connection is
provided whenever there is a risk of product crystallization or solids
deposition in the spring chamber.
Shutdown flushing (option)
This shaft seal flushing variant is used
in service environments involving a risk of solids deposition, crystallization
of the fluid pumped or blockage problems in the pump interior. It can be
combined with the MUNSCH-REA-F/D double mechanical seal.
Continuous flushing (option)
The continuous shaft seal flushing
variant ensures reliable protection when pumping fluids carrying high solids
loads or dissolved gases, when the fluid is pumped near its boiling point or
when there is a risk of the pump running dry.
MUNSCH-REA-F/D double mechanical seal
The double mechanical seal is employed
whenever there is a risk of solids deposition or product crystallization, in
service environments posing a health or environmental hazard or when the fluid
is pumped near its boiling point or dry running cannot be ruled out with a
single mechanical seal. MUNSCH-REA-F/D double mechanical
seals can be operated with a buffer fluid in the once-through mode, with
closed-circuit thermosyphon buffer systems or quench systems.
The mechanical seal pumps are also suited for use in
explosive atmospheres (ATEX) and meet the requirements of EU
Directive 94/9/EC.
Flushing options for Munsch
mechanical seals
NP REA F/FD
NP-B REA F/FD
Flushing
connection detail:
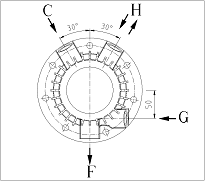
Seal type
|
Flushing
variant
|
Connec-tions
|
Flushing
liquid specifications
|
Source
|
Notes
|
REA F
|
Spring chamber flushing
|
H => F
|
Free from solids,
product-compatible, non-corrosive, normally tap
water
|
Site supply system
|
Atmospheric flushing
|
Conti-nuous flushing
|
C
|
Free from solids,
product-compatible, non-corrosive
Flow rate:
0.9 – 1.5 l/min. Pressure:
max. 10bar.
|
|
|
Shut-down flushing
|
C
|
Free from solids,
product-compatible, non-corrosive
Flow rate:
5 – 8 l/min. Pressure: max.
10bar.
|
Site supply system
|
|
REA
F/D
|
Conti-nuous flushing with
buffer fluid from an external source
(pressurized)
|
G => H
|
Free from solids,
product-compatible, non-corrosive, max.
kinematic viscosity 15 mm²/s, minimum flow rate
0.25 l/min, max. outlet temperature 60°C, max.
temperature gradient between inlet and outlet 25
K, temperature below boiling point
|
Site supply system
|
Suitable buffer fluids:
water
Recommended flow rate:
0.5 l/min.
|
Buffer fluid with
thermo-syphon tank in the recircu-lating mode
|
G => H
|
Free from solids and
crystallizing components, product-compatible,
high-boiling, good lubricating characteristics,
environmentally compatible, max. kinematic
viscosity 5 mm²/s, max. outlet
temperature 60°C, max. temperature
gradient between inlet and outlet 25 K,
temperature below boiling point
|
Thermosyphon tank,
pressurized
|
Suitable buffer fluids:
water, vegetable oil, glycol-water
mixture.
Sealing pressure > pressure
on product side of mechanical seal. Hosing to be
installed with a rising/falling slope. Tank to
be installed at a level of 1.5 to 2m above the
mechanical seal. Avoid
horizontal runs.
|
Buffer-fluid in the
continuous-flow mode (un-pressurized)
|
G => H
|
Free from solids,
product-compatible, non-corrosive, max.
kinematic viscosity 15 mm²/s, minimum flow rate
0.25 l/min, max. outlet temperature 60°C, max.
temperature gradient between inlet and outlet 25
K, temperature below boiling point
|
Site
supply system
|
Atmospheric flushing
|
Quench
|
G => H
|
Free from solids and
crystallizing components,
product-compatible, high-boiling, good
lubricating characteristics, environmentally
compatible, max. kinematic viscosity 5 mm²/s,
max. outlet temperature
60°C, max. temperature
gradient between inlet and outlet 25 K,
temperature below boiling point
|
Quench tank, operated in the
unpressurized recirculating mode
|
Atmospheric flushing with
atmosphere-side mechanical seal operated as
quench seal. Quench tank to be installed at a
level of 1 m - 2m above the mechanical seal.
Hosing to be installed with a
rising/falling slope. Avoid horizontal runs.
|
Continuous flushing
|
C
|
Free from solids,
product-compatible, non-corrosive
Flow rate:
0,9 – 1,5 l/min. Druck:
max. 10bar.
|
|
|
Shutdown flushing
|
C
|
Free from solids,
product-compatible, non-corrosive
Flow rate:
5 – 8 l/min. Pressure:
max. 10bar.
|
|
|
NP REA C/CD
Flushing
connection detail:
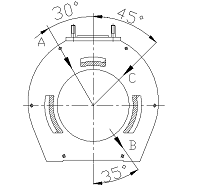
Seal type
|
Flushing
variant
|
Connections
|
Flushing
liquid specifications
|
Source
|
Notes
|
REA C
|
Spring chamber flushing
|
C => B
|
Free from solids,
product-compatible, non-corrosive, normally tap
water
|
Site supply system
|
Atmospheric flushing
|
Continuous flushing
|
A
|
Free from solids,
product-compatible, non-corrosive
Flow rate:
0.9 – 1.5 l/min. Pressure:
max. 10bar.
|
|
|
Shutdown flushing
|
A
|
Free from solids,
product-compatible, non-corrosive
Flow rate:
5 – 8 l/min. Pressure:
max. 10bar.
|
Site supply system
|
|
REA
C/D
|
Flushing
with pressurized buffer fluid
|
C => B
|
Free from solids,
product-compatible, non-corrosive, max.
kinematic viscosity 15 mm²/s, minimum flow rate
0.25 l/min, max. outlet temperature 60°C, max.
temperature gradient between inlet and outlet 25
K, temperature below boiling point
|
Site supply system
|
Suitable buffer fluids:
water
Recommended flow rate: 0.5
l/min.
|
|
B => C
|
Free from solids and
crystallizing components, product-compatible,
high-boiling, good lubricating characteristics,
environmentally compatible, max. kinematic
viscosity 5 mm²/s, max. outlet
temperature 60°C, max. temperature
gradient between inlet and outlet 25 K,
temperature below boiling point
|
Thermosyphon tank,
pressurized
|
Suitable buffer fluids:
water, vegetable oil, glycol-water
mixture.
Sealing pressure > pressure
on product side of mechanical seal.
Tank to be installed at a level of 1.5 to
2m above the mechanical seal.
Hosing to be installed with a
rising/falling slope. Avoid horizontal runs.
|
Flushing
in once-through mode
|
B => C
|
Free from solids,
product-compatible, non-corrosive, max.
kinematic viscosity 15 mm²/s, minimum flow rate
0.25 l/min, max. outlet temperature 60°C, max.
temperature gradient between inlet and outlet 25
K, temperature below boiling point
|
Site supply system
|
Atmospheric flushing
|
Quench
|
B => C
|
Free from solids and
crystallizing components,
product-compatible, high-boiling, good
lubricating characteristics, environmentally
compatible, max. kinematic viscosity 5 mm²/s,
max. outlet temperature
60°C, max. temperature
gradient between inlet and outlet 25 K,
temperature below boiling point
|
Quench tank
|
Atmospheric flushing with
atmosphere-side mechanical seal operated as
quench seal. Quench tank to be installed at a
level of 1 m - 2m above the mechanical seal.
Hosing to be installed with a rising/falling
slope Avoid horizontal runs.
|
Continuous flushing
|
A
|
Free from solids,
product-compatible, non-corrosive
Flow rate:
0.9 – 1.5 l/min. Pressure:
max. 10bar.
|
|
|
Shutdown flushing
|
A
|
Free from solids,
product-compatible, non-corrosive
Flow rate:
5 – 8 l/min. Pressure:
max. 10bar.
|
|
|
NPC REA F/FD
NPC-B REA F/FD
Flushing connection detail:
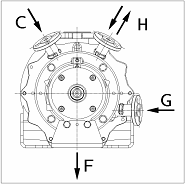
Seal type
|
Flushing
variant
|
Connections
|
Flushing
liquid specifications
|
Source
|
Notes
|
REA F
|
Spring chamber flushing
|
H => F
|
Free from solids,
product-compatible, non-corrosive, normally tap
water
|
Site supply system
|
Atmospheric flushing
|
Continuous flushing
|
C
|
Free from solids,
product-compatible, non-corrosive
Flow rate:
0.9 – 1.5 l/min. Pressure:
max. 10 bar.
|
|
|
Shutdown flushing
|
C
|
Free from solids,
product-compatible, non-corrosive
Flow rate:
5 – 8 l/min. Pressure: max.
10 bar.
|
Site supply system
|
|
REA F/D
|
Flushing
with pressurized buffer fluid
|
G => H
|
Free from solids,
product-compatible, non-corrosive, max.
kinematic viscosity 15 mm²/s, minimum flow rate
0.25 l/min, max. outlet temperature 60°C, max.
temperature gradient between inlet and outlet 25
K, temperature below boiling point
|
Site supply system
|
Suitable buffer fluids:
water
Recommended flow rate:
0.5 l/min.
|
|
G => H
|
Free from solids and
crystallizing components, product-compatible,
high-boiling, good lubricating characteristics,
environmentally compatible, max. kinematic
viscosity 5 mm²/s, max. outlet
temperature 60°C, max. temperature
gradient between inlet and outlet 25 K,
temperature below boiling point
|
Thermosyphon tank,
pressurized
|
Suitable buffer fluids:
water, vegetable oil, glycol-water
mixture.
Sealing pressure > pressure
on product side of mechanical seal. Tank to be
installed at a level of 1.5 to 2m above the
mechanical seal. Hosing
to be installed with a rising/falling slope.
Avoid horizontal runs.
|
Flushing
in once-through mode
|
G => H
|
Free from solids,
product-compatible, non-corrosive, max.
kinematic viscosity 15 mm²/s, minimum flow rate
0.25 l/min, max. outlet temperature 60°C, max.
temperature gradient between inlet and outlet 25
K, temperature below boiling point
|
Site supply system
|
Atmospheric flushing
|
Quench
|
G => H
|
Free from solids and
crystallizing components,
product-compatible, high-boiling, good
lubricating characteristics, environmentally
compatible, max. kinematic viscosity 5 mm²/s,
max. outlet temperature
60°C, max. temperature
gradient between inlet and outlet 25 K,
temperature below boiling point
|
Quench tank
|
Atmospheric flushing with
atmosphere-side mechanical seal operated as
quench seal. Quench tank to be installed at a
level of 1 m - 2m above the mechanical seal.
Hosing to be installed with a
rising/falling slope. Avoid horizontal runs.
|
Continuous flushing
|
C
|
Free from solids,
product-compatible, non-corrosive
Flow rate:
0.9 – 1.5 l/min. Pressure:
max. 10 bar.
|
|
|
Shutdown flushing
|
C
|
Free from solids,
product-compatible, non-corrosive
Flow rate:
5 - 8
l/min. Pressure
max. 10 bar.
|
|
|
|